Business Process Management (BPM) is a complex set of disciplines dealing with processes that are part of a business. Even though we covered business process automation, that’s just part of BPM, which also includes discovering, modeling, analyzing, measuring, and optimizing processes with the ultimate goal to improve how a business operates, cut costs, and more.
To explain what Business Process Management really is, it’s important to start small, and the smallest unit of BPM is a process. So, what exactly is a process, how is it determined, and what are its elements? Also, what methods are used to determine a process, and how is a process represented? Read on to find out.
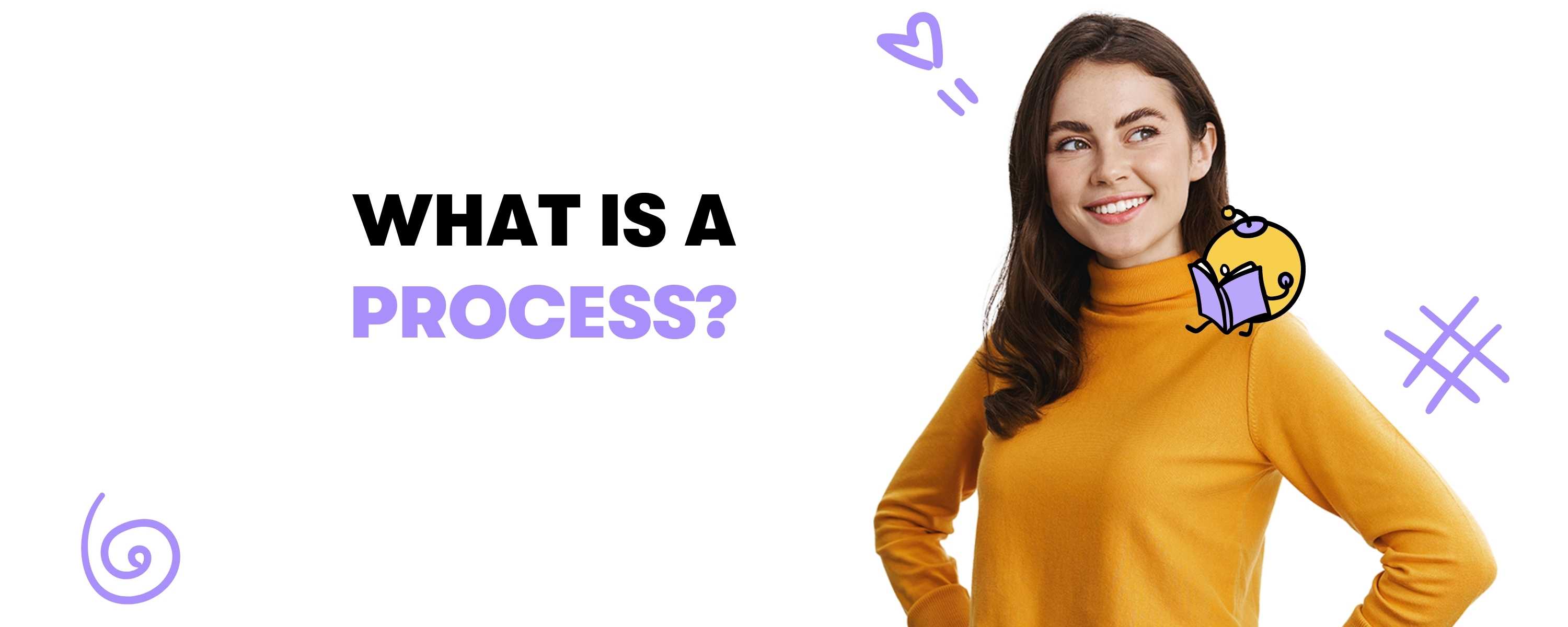
What is a Process?
Dictionaries describe the term process as a set of steps or actions one needs to take to achieve a particular goal. This is quite an accurate description, but what we’re looking for is a description of a business process.
Luckily, the definition doesn’t differ that much. A business process can be described as a series of steps that need to be taken to complete a certain business goal, such as developing a product or executing a service. Every business process consists of structured activities that need to be done to complete a goal.
We already used Ford’s moving assembly line on several occasions, but it perfectly represents a business process. Each worker only focuses on one part of the process until the entire car is put together.
Of course, some processes aren’t that complex, as not every business process is created with a goal to develop a product from start to finish. In fact, business processes can be divided into three big groups:
- Operational Processes — These are directly related to developing and maintaining your product or service.
- Supporting Processes — These are indirectly directed but still pertain to your product or service.
- Management Processes — These have nothing to do with what you do but are important for making your business work well. A good example would be an employee onboarding process.
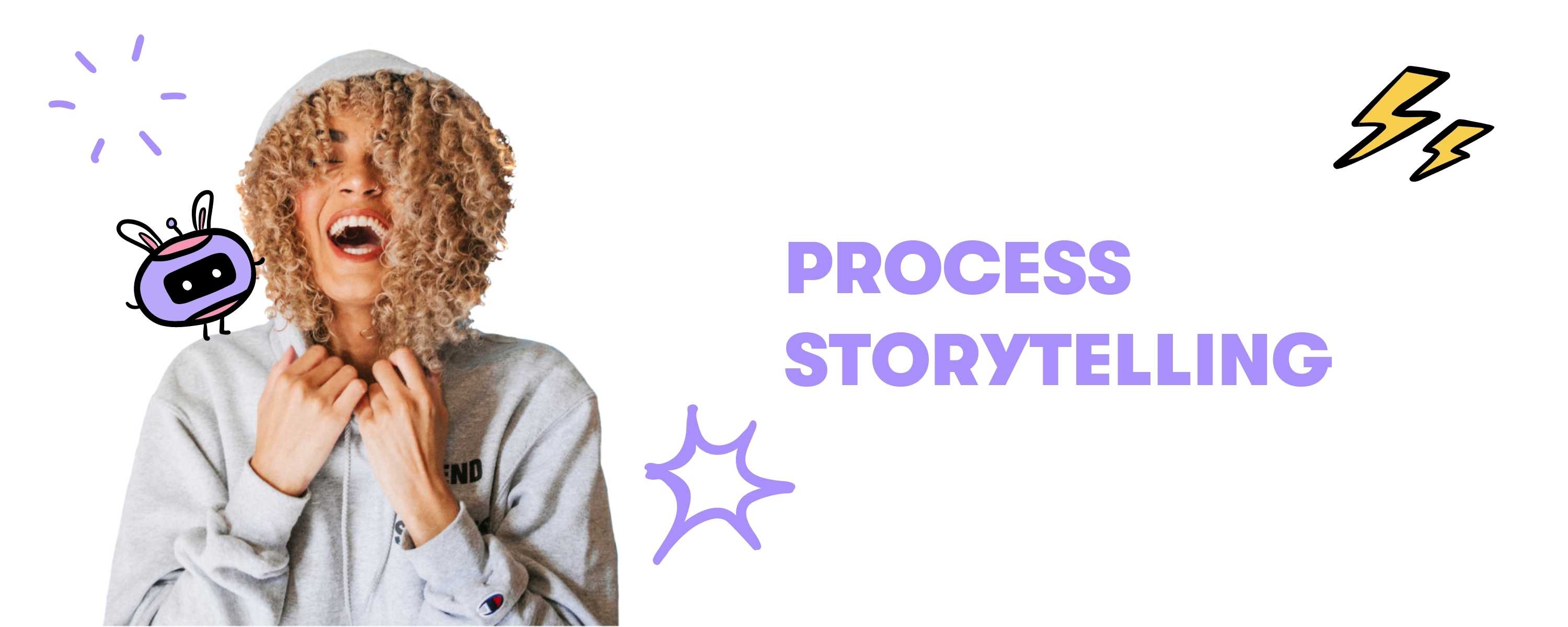
Process Storytelling: A Good Story is Half the Work
Modeling a process is one of the essential practices in business process management. Its goal is to be able to deduct steps required for the process to work and serve its purpose. There are several ways to model a process, but one method stands out as the most successful — the process storytelling method.
Storytelling is as old as humankind. Our brains are hardwired to remember certain elements of a story that make it unique, such as characters, their purposes, problems and challenges, and more. That’s the similar approach we want to assume for process modeling — we want to build a story around it. Stories have been used to convey context and essential information in a simple and meaningful way, which is why such an approach is perfect for business processes.
Here’s an example of how a process story looks like:
- People — Who are the characters? Who is the protagonist of the story (process)?
- Process name — What’s the best title for your story that will briefly convey its essence?
- Process purpose — Why are we doing what we’re doing? What’s the goal? What’s the purpose?
- Pain points — What are the possible challenges for your story? What would the characters encounter as the possible issue?
By answering each of the questions, you’ll be able to provide adequate context for the process and convey additional meaning in a simple and engaging way.
You’ll still have to provide enough information to your business that doesn’t have to focus on the story that much.
- Department — What department should work on the process?
- Connected systems — Are there any systems that are required in the process?
- Improvement potential — How can the process improve your business?
The last step is to go through the process lifecycle, which we’ll explain in a while.
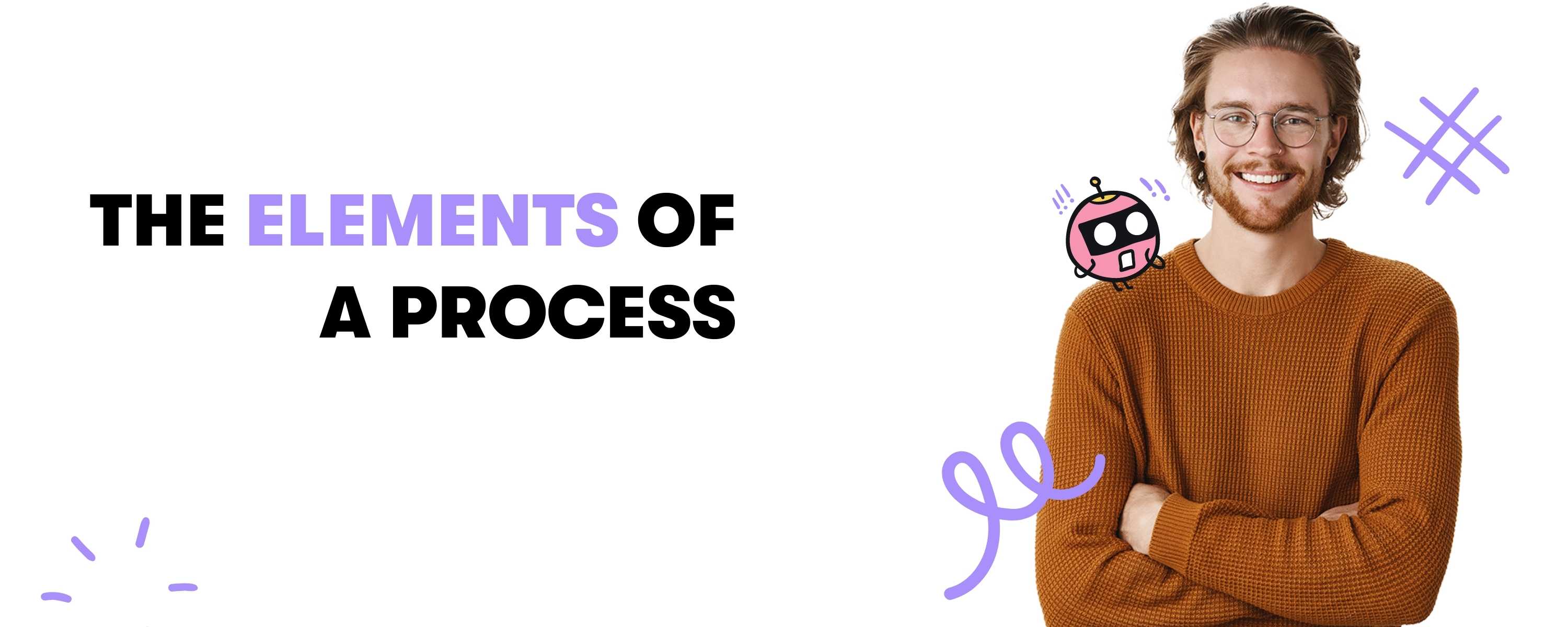
The Elements of a Process
Now that we know the definition of a business process, it’s necessary to describe some of its characteristics that will help you understand how processes relate and improve businesses. It’s essential to adopt a holistic approach to processes, meaning not only to view them in their current state but also to include their future changes, and the following six attributes can help you with that.
Frequency and Effort
First of all, it’s important to determine how often the process at hand will be executed. Some processes are executed several times a day, and others are daily, weekly, monthly, or annual processes.
Also, it’s essential to know how much effort you’ll need for the process. Will it take just one or two employees or an entire department?
Process Flow
Next, you need to determine the flow of your process by pointing out the essential steps that are part of it. Of course, you’ll have to provide the names of participants and the tasks they ought to perform, as well as the systems that will be included in the process. It’s also important to determine the data flow in the process.
This is important because sometimes you may have two identical processes in terms of steps, but the actors and systems will be completely different.
Rules and Exceptions
Sometimes, you won’t have complete freedom to model and develop a process. Your business might have some internal rules you’ll have to stick to. On top of that, there might be certain legal constraints that you’ll have to take into account before modeling a process, so it’s wise to take them into account as well.
Also, every business process is the ideal view of the process. However, when put into practice, there are often exceptions that you’ll have to integrate into your model to improve efficiency and be aware of the possible challenges. Exceptions are very important if you decide to automate the process, as automation might not be possible without addressing them.
Infrastructure
Most of your processes will be digital, meaning you’ll have to rely on certain infrastructure to run them. In fact, you’ll have to take into account all the systems that will be connected to your business process and incorporate them adequately, depending on whether they are internal, external, cloud-based, SaaS, or more.
Pinning down infrastructure is also relevant to be able to apply automation properly and cut down on unnecessary work that bots can conduct.
Data Security
You want to keep the security levels at maximum regardless of the process, so it’s important to address the issue of data security as different processes require different approaches.
Stability
Finally, it’s important to have a general overview of the stability of the process. To determine that, you can decide whether the process or some of its elements would require changing in the next period. It’s important to detect the variables that could change over time and affect stability and try to mitigate them.
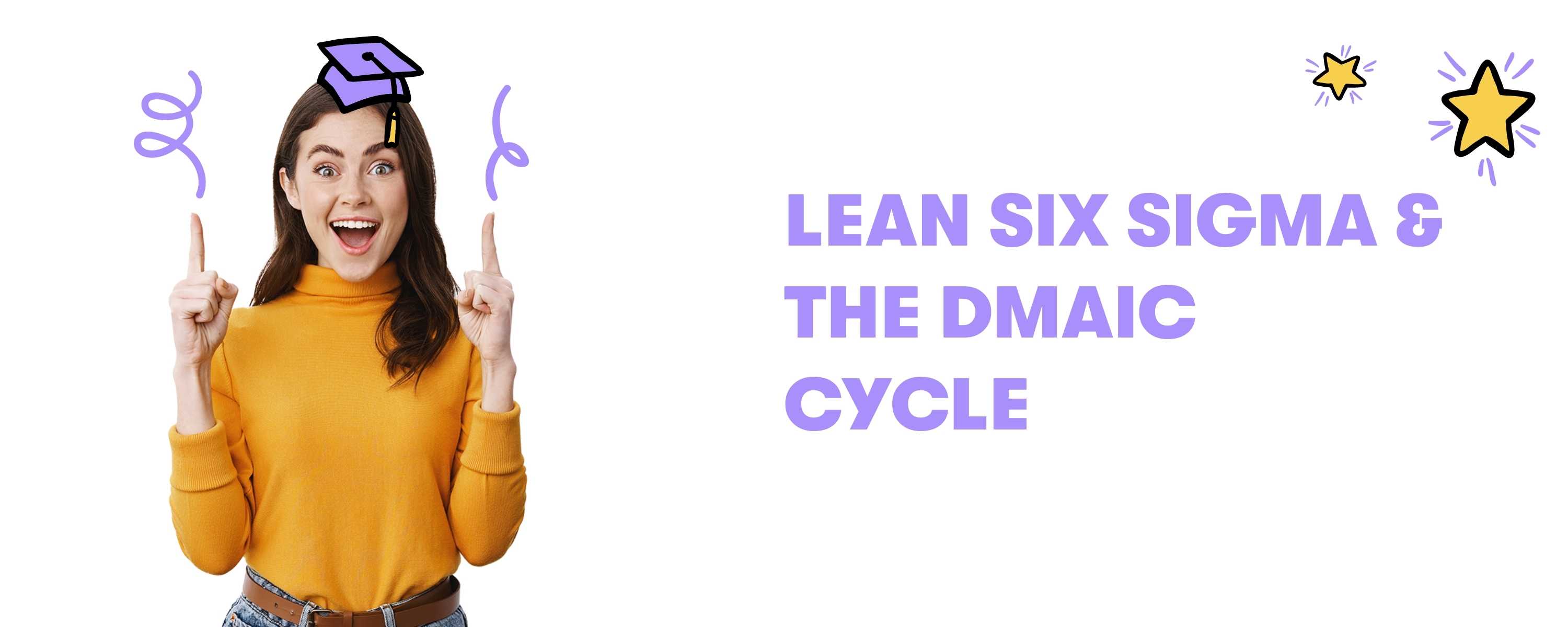
Lean Six Sigma and the DMAIC Cycle
Several approaches to process improvement are used around the globe, but Lean Six Sigma remains the most powerful and consistently productive one.
Lean Six Sigma is a method used in business process management that aims to improve the performance of businesses by removing waste in a systematic way and reducing variation. It’s a combination of lean manufacturing/enterprise and Six Sigma.
Six Sigma was developed in Motorola in the US in 1975 as a competitor to Japanese lean methodology (also known as kaizen). However, Lean Six Sigma was developed much later, during the 2000s, and became a stand-alone approach, even though many ideas were based on lean, which was developed as part of the Toyota Production System in the 50s.
Lean Six Sigma is a perfect management approach for data-driven process improvement and is one of the essential elements of the automation mindset since it’s focused on continuous improvement.
The popular approach focuses on DMAIC phases which are taken from Six Sigma. Instead of making big changes monthly or annually, DMAIC focuses on making small daily changes, improving the process iteratively.
DMAIC is actually an acronym standing for: Define, Measure, Analyze, Improve, and Control.
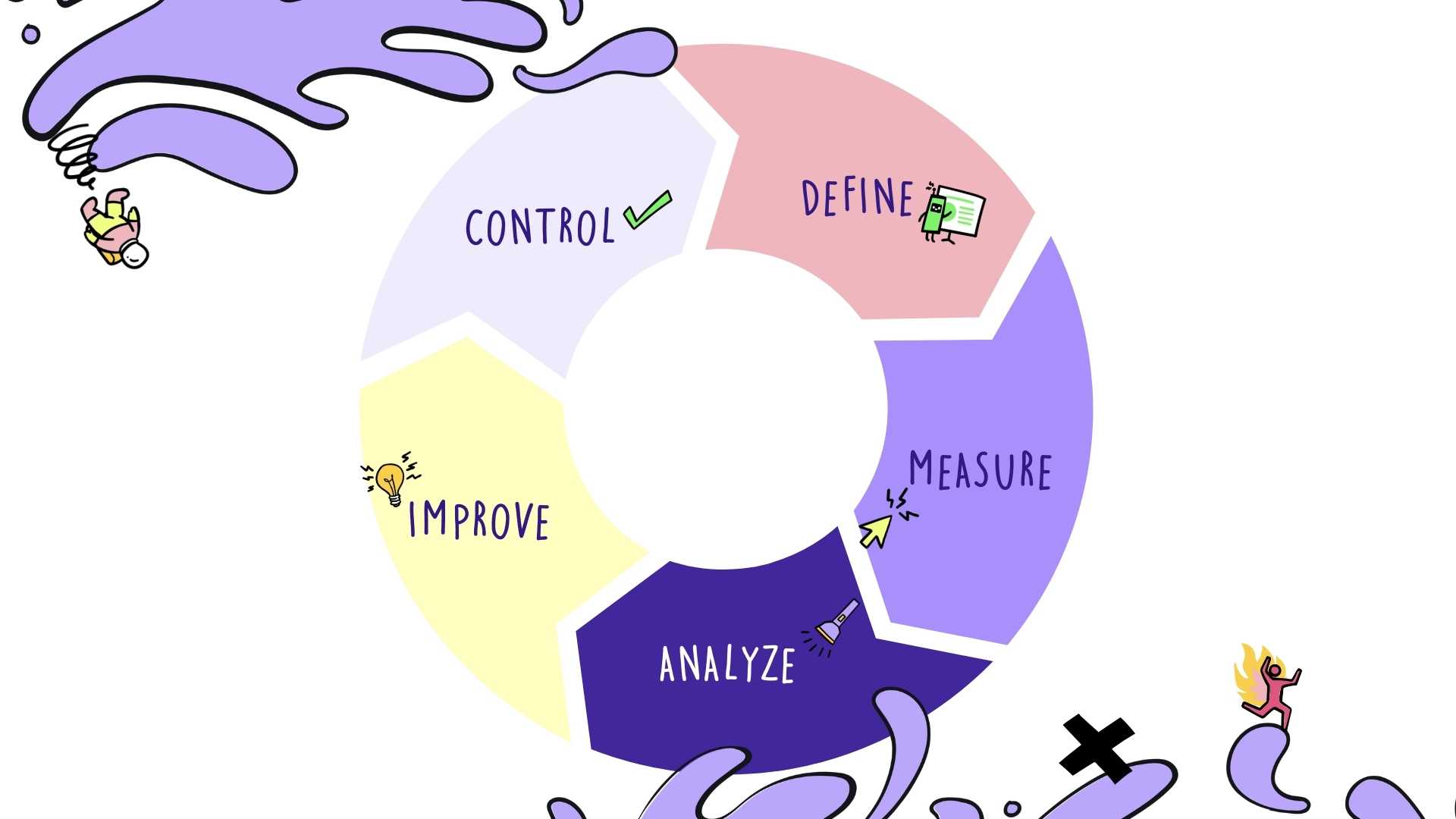
Define
The first step is to clearly define the problem/challenge, goal, resources, scope, and timeline. It needs to be well-defined and precise, and without the use of technology, defining the challenge often depends on the decision holder.
Measure
To be able to follow the process and continuously upgrade it, it’s important to identify key performance indicators (KPIs) and make the process as quantifiable as possible. Simply ask yourself: what do you want to pay close attention to? Once you know the answer, find a way to measure it.
To proceed with the other three steps and eventually automate the process, it’s important to get the right information from the key process stakeholders at the right time. This is a complex communication issue that takes a lot of time in traditional processes. However, thanks to technologies such as process mining, it’s much easier to control and measure quantifiable data daily, making the entire method even leaner.
Analyze
Once you have enough data from the KPIs you defined, it’s time to analyze them and address possible challenges or ongoing problems. The numbers will often tell you the root cause.
Improve
At this step, you’ll have to identify, test, and implement the solution to the problem discovered during the analysis. This could be as easy as changing the parameters of the process when the process itself is automated.
Control
Once the changes are made, it’s important to see how they operate in practice by controlling them and measuring their impact on KPIs. Control is also essential for ensuring that the implemented solution is sustainable.
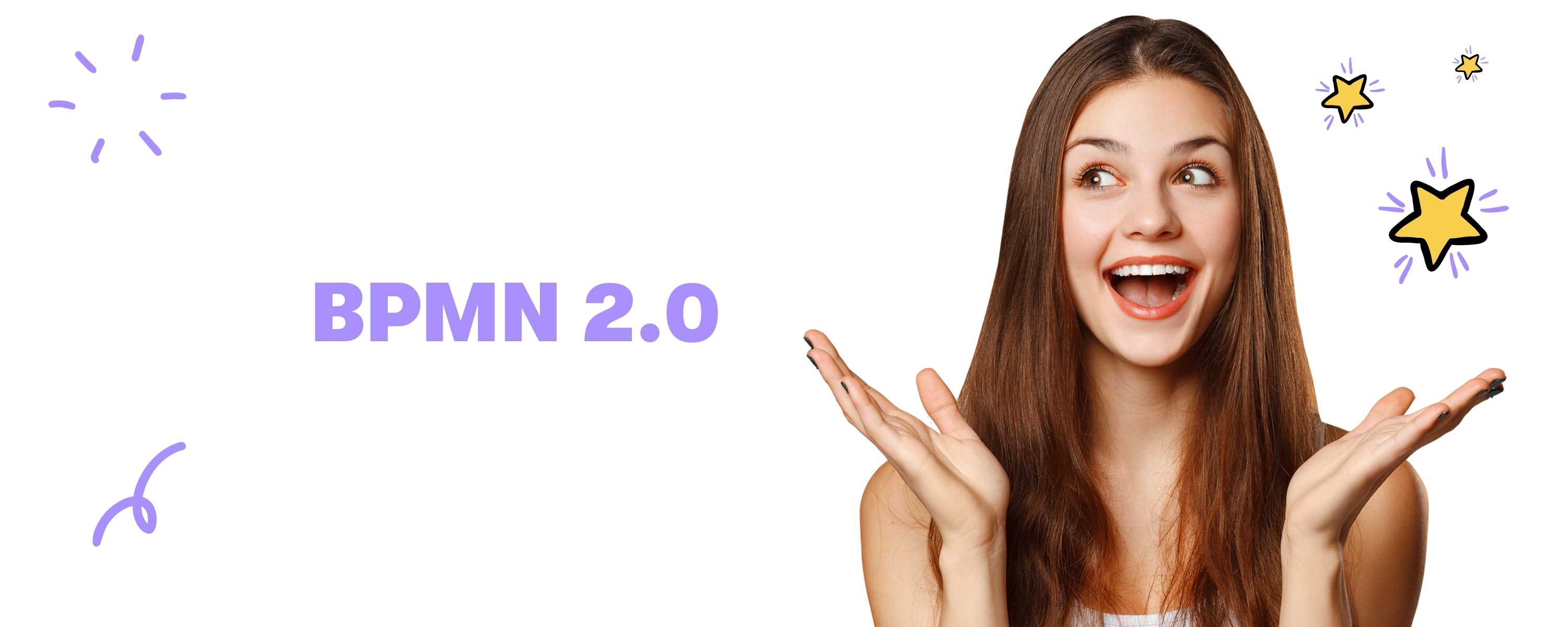
BPMN 2.0: The Way of the Process
A business process model needs to be represented in a way, and that’s where Business Process Model and Notation come in — it’s a graphical representation of the process in a business process model.
BPMN was created by the Business Process Management Initiative (BPMI) and maintained by the Object Management Group (OMG). The graphical representation was updated in 2011, and version 2.0 was named Business Proces Model and Notation since semantics was introduced in the 2.0 version. BPMN is is a specification maintained by BPM, but it’s also ratified as an ISO standard, number 19510.
Essentially, BPMN is made for everyone who is involved in implementing the process, giving them the necessary details for the implementation process. Since all stakeholders in a process come from different backgrounds, many of them non-technical, everyone needs to learn the standardized common language used in BPMN. In a way, BPMN makes it possible for different departments to communicate about the project, which now has a higher level of transparency thanks to BPMN.
The graphical representation bridges the gap between planning the project and actually implementing it in your business. In addition to that, it helps all stakeholders have a better overview and understanding of the process. Consequently, everyone can analyze the process easily, gain insights, and optimize it to make it more effective. If you want to know witch which BPM tool to start, have a look here.